
The relative phases of these currents are chosen so that they should result in a smoothly rotating current space vector that is always in the quadrature direction with respect to the rotor and has constant magnitude. Sinusoidally commutated brushless motor controllers attempt to drive the three motor windings with three currents that vary smoothly and sinusoidally as the motor turns. Shaft Torque = 1.5I 0 * Kt (a constant independent of the shaft angle).If the phase currents are sinusoidal: I R = I 0 Sino I S = I 0 Sin (+120o) I T = I 0 Sin (+240o) this reduces to: I R, I S and I T are the phase currents.Kt is the torque constant of the motor and.o is the electrical angle of the shaft,.This is because the torque produced in a three phase brushless motor (with a sine wave back-EMF) is defined by the following equation: Sinusoidal commutation solves this problem. Trapezoidal commutation is inadequate to provide smooth and precise motor control of brushless dc motors, particularly at low speeds. The trapezoidal-current drive systems are popular because of the simplicity of their control circuits but suffer from a torque ripple problem during commutation. Back-EMF sensors that sense the back EMF in the unconnected winding can be used to achieve the same results In motor applications such as air conditioners and refrigerators use of Hall-Effect sensors is not a viable option. This produces a current space vector that approximates smooth rotation as it steps among six distinct directions as the rotor turns. The current waveform for each winding is therefore a staircase from zero, to positive current, to zero, and then to negative current. One of the simplest methods of control for dc brushless motors uses what is termed Trapezoidal commutation.įigure 2: Trapezoidal Control: Drive Waveforms and Torque at commutation In a BLDC motor, the MCU must know the position of the rotor and commutate at the appropriate time. The commutation of the power transistors energizes the appropriate windings in the stator to provide optimum torque generation depending on the rotor position. The variable voltage can be used to control the speed of the motor and the available torque. When properly commutated, the torque-speed characteristics of the BLDC motor are identical to a dc motor. The effective voltage is proportional to the PWM duty cycle.
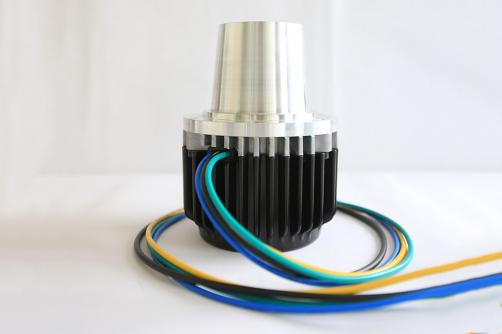
Pulse-width modulation is used to apply a variable voltage to the motor windings.
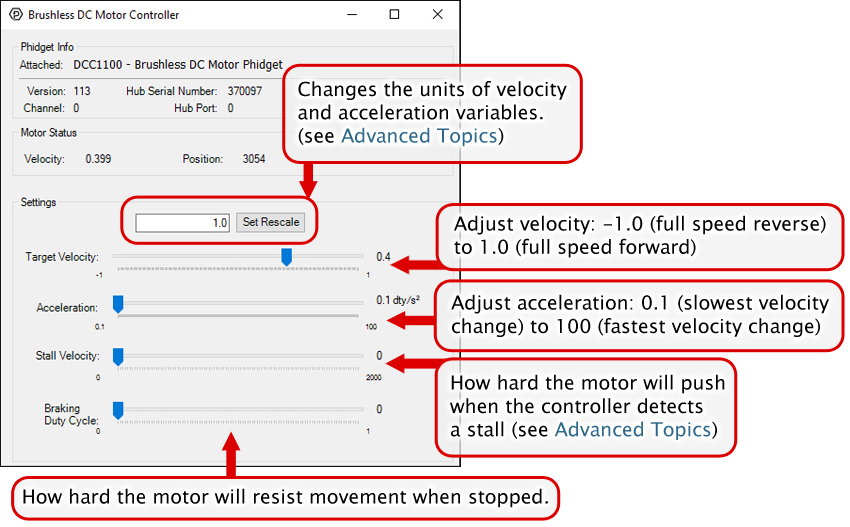
Method to estimate the rotor position using the back-EMF or Hall Sensors.The control algorithm must provide three things: High-power motors must use PWM control and require a microcontroller to provide starting and control functions. This is not practical when driving higher-power motors. Typically, the motor voltage is controlled using a power transistor operating as a linear voltage regulator. Many different control algorithms have been used to provide control of BLDC motors. Refrigerator and air conditioning compressors also require sensorless control when using BLDC motors. Sensorless control is essential for low-cost variable speed applications such as fans and pumps. Sensorless BLDC control eliminates the need for Hall effect sensors, using the back-EMF (electromotive force) of the motor instead to estimate the rotor position. This results in more wires and higher cost.

To sense the rotor position BLDC motors use Hall Effect sensors to provide absolute position sensing. If the application requires servo-positioning, dynamic braking, or dynamic reversal, it is recommended that complementary center-aligned PWM signals be used. Most applications, that only require variable speed operation, will use six independent edge-aligned PWM signals. For closed-loop speed control there are two additional requirements, measurement of the motor speed and/or motor current and PWM signal to control the motor speed and power.īLDC motors can use edge-aligned or center-aligned PWM signals depending on the application requirements.
